Technology
The name “textile lighting systems” comes from the fact that textile materials are used as the light guide; it is not because they are used in textile end products. The incredible flexibility of this technology makes it particularly well suited for integrating light into textile applications. But that’s not all: since it is easy to assemble and can be folded into (almost) any shape, it also gives outstanding results in non-textile products. This particularly applies in the case of complicated installation spaces where other technologies reach their limits.
In their basic design, textile lighting systems consist of one or more LED light sources and a textile material – individual fibres or a fabric acting as the light guide. With such a fabric, clear plastic optical fibres or POFs made from PMMA are used, which, as weft threads, are woven with warp threads made from white polyester to form light-guiding fibre mats. The light-guiding individual fibres of the fabric are combined together in a ferrule with which they are connected to the LED modules.
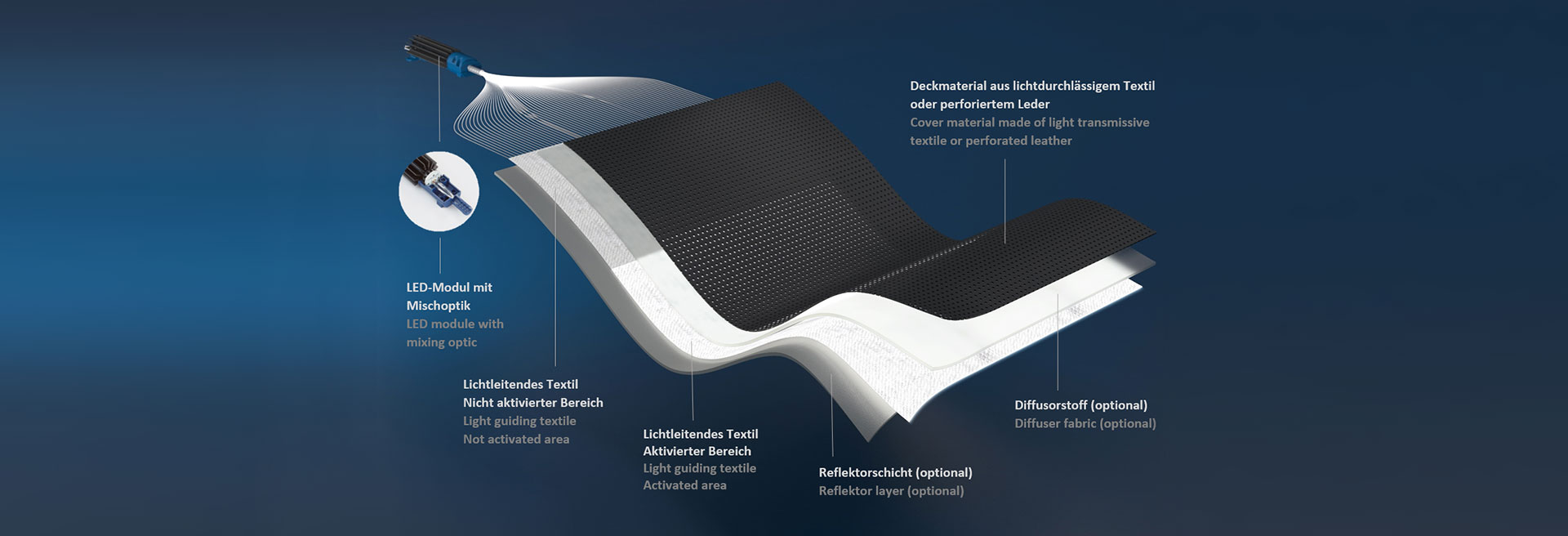
The light is usually emitted at the side of the fibre or fabric (lateral emission). The emission is activated at the desired light output areas, i.e. the fabric is specifically provided with individual light-scattering surface structures. A top fabric is placed over the light-guiding fibre mat. Optionally, a diffusor fabric and a reflector layer can also be used. If you do not activate the fibre mat, the light is emitted at the end of the fibre mat. You use such an axial emission to implement linear lighting.
The LED modules that are designed for use in textile lighting systems consist of the integrated LED – monochrome, white or RGB – the LED driver and thermal elements. A special mixer optic is placed in front of the LED that ensures that the LED’s light is distributed optimally to all polished fibre ends.
Textile lighting solutions are ideal in both small and large-scale production for illuminating large areas, for free-form shapes and for achieving dynamic light. Compared with other technologies, they offer a number of relevant advantages.
The advantages of textile lighting solutions
Optimal use of the installation space
The technology of textile lighting solutions enables the installation space of the light guide to be separated flexibly from that of the electronics components. The light guide itself does not even need 5 mm for its entire design and it can be folded into (almost) any shape. This flexibility in terms of the installation space can be used not just in the development of new products, it also opens up possibilities for product upgrades as part of facelifts or relaunches. The new technology enables system integration with minimal adjustments to the subsequent fusion processes in existing products and production processes. This means that light can be integrated into products where this is hardly possible with other technologies.
Initial investments and unit costs
In contrast to today’s commonly used plastic injection moulding technology, implementing textile lighting solutions does not involve any component-specific tool investment. This makes them extremely cost-effective for small-scale production. The commercial benefits of plastic injection moulding lie in the direct unit costs with large-scale production. However, as illuminated surfaces become larger, these advantages are becoming increasingly less significant. Since the costs of injection moulding tools increase exponentially with the size of the light guide, this makes a solution that is based on textile light guides even more cost effective the larger the area to be illuminated becomes.
Short development times –
fast prototyping
The light guide as a textile roll-to-roll product is virtually a COP part from a materials engineering perspective, which is re-assembled by adapting the process parameters for the relevant customer application.
This tool-free technology and the availability of suitable electronic and LED modules enables extremely short development times. Fast prototyping and, therefore, early visualisation that is almost ready for series production are also possible. This also makes changes to the design at a late development stage considerably easier or even possible in the first instance. In this way, the development and decision-making processes can be streamlined and accelerated significantly.
Dynamic light
If you assign individual fibres or bundles of fibres to different LED modules, this creates fascinating opportunities for dynamic lighting scenarios. These cannot be achieved by using other technologies, or else only with great effort and enormous costs..
Crash test – no problem
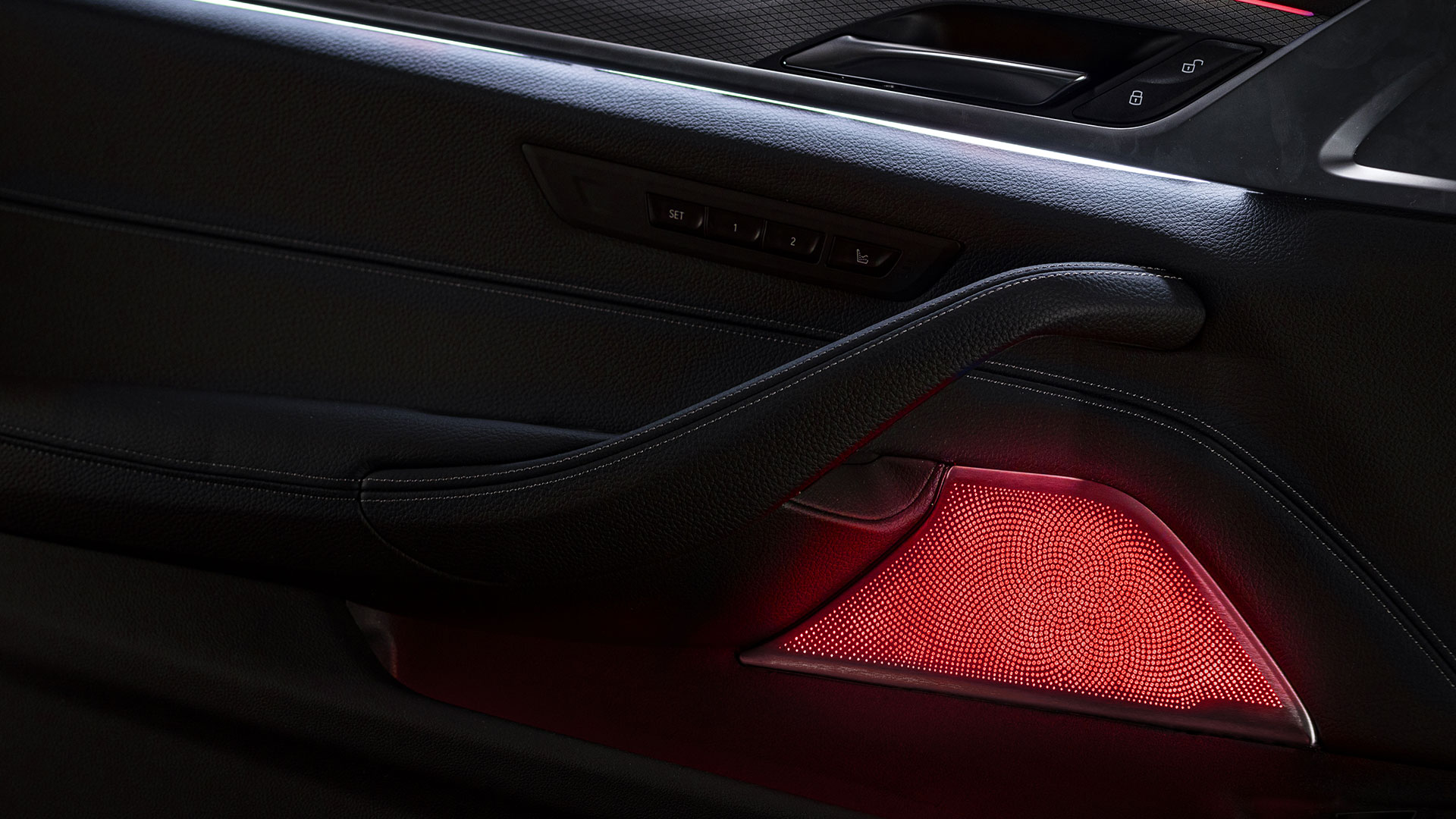
A particularly significant advantage of textile lighting systems for the automotive industry is their flexibility, enabling them to be integrated even in crash-sensitive zones. This enables larger surfaces in vehicle areas to be illuminated, which would not be permissible with other technologies.